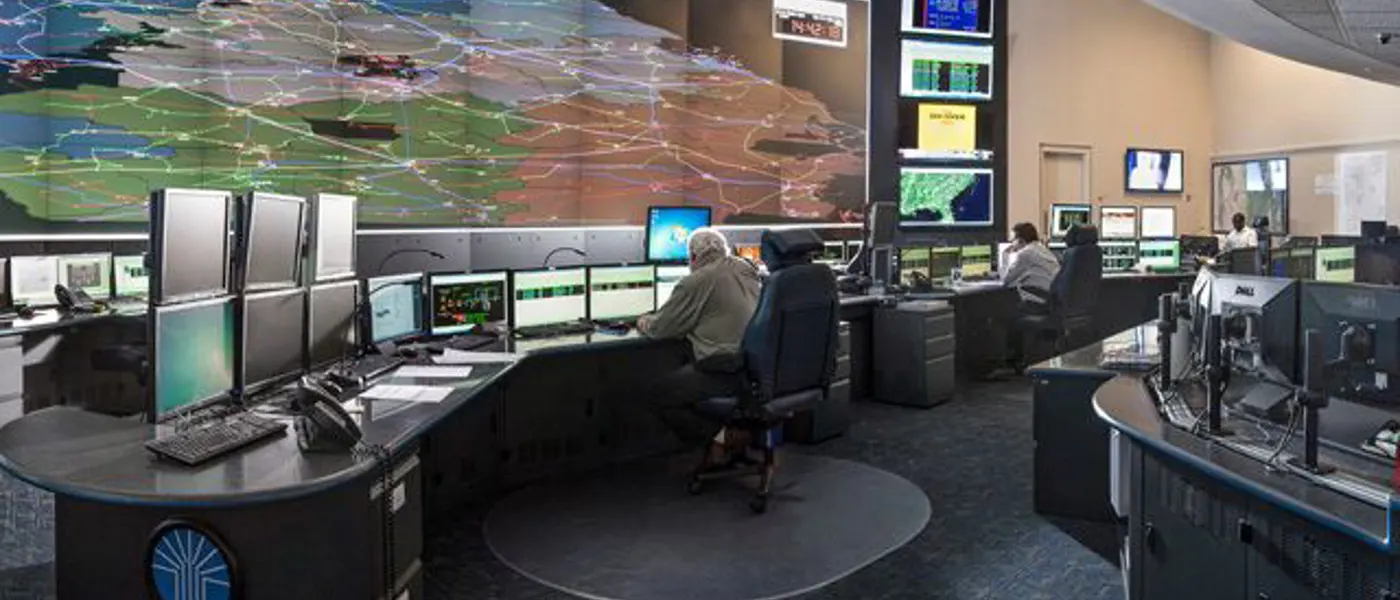
Georgia System Operations Corporation
Georgia System Operations Corporation Takes Control
Georgia System Operations Corporation (GSOC) controls and monitors electric generation, transmission and distribution assets for one of the largest electric cooperatives in North America. An independent system operations company, GSOC serves 39 of Georgia’s distribution electric membership corporations (EMCs), Oglethorpe Power Corporation (OPC) and Georgia Transmission Corporation (GTC).
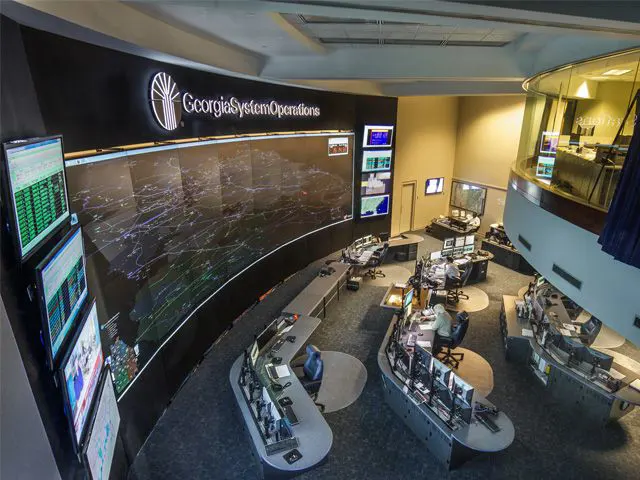
GSOC is charged with monitoring thousands of miles of transmission line on behalf of GTC for both routine maintenance and outages due to severe weather. GSOC coordinates the switching and scheduling when a portion of the line needs to be removed from service for maintenance and helps restore electric service throughout the state when outages occur. On the power generation side, the company also monitors and controls several power plants for Oglethorpe Power, helping balance the load to meet the energy demand of its members.
Recently, GSOC upgraded its control centers as part of the company’s ongoing Smart Grid projects intended to modernize operations and provide greater situational awareness. The upgrade encompassed every aspect of the two control centers, from the carpet on the floor to the lights in the ceiling and everything in between. One of the primary needs for the upgrade included new control room consoles to house the equipment for a new energy control system.
While the console is a showpiece, it also had to be functional, because we’re operating billions of dollars worth of equipment for our affiliated companies and keeping the lights on for cooperatives throughout Georgia
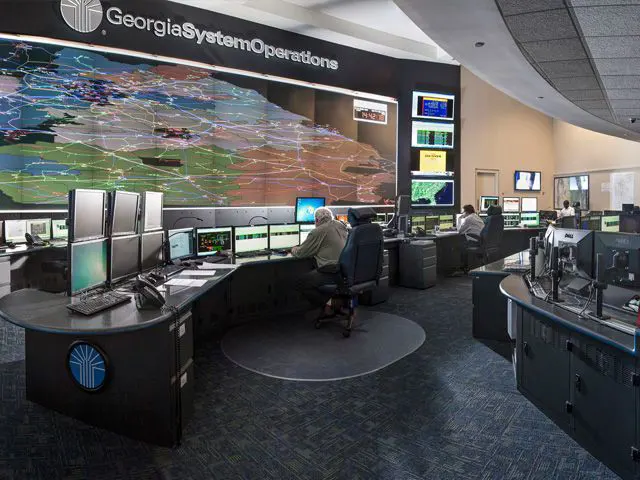
Lloyd Snyder, manager of transmission operations for GSOC, served as project manager for the control center upgrade and was charged with finding the right consoles. “We looked at a number of consoles. This isn’t the first control center I’ve built, so I was familiar most products out there,” said Snyder. “Still, I flew around the country looking at different control centers that had either just been built or were under construction.”
Like many control rooms, the GSOC control centers are a showpiece for the company. It’s the destination for all sorts of visitors and dignitaries, so the consoles needed to make a good impression. “While the console is a showpiece, it also had to be functional, because we’re operating billions of dollars worth of equipment for our affiliated companies and keeping the lights on for cooperatives throughout Georgia,” said Snyder.
Ergonomics was a key requirement of the new console design. Operators sitting at the consoles work 12-hour shifts and some have up to 13 monitors in front of them. That’s just at their workstation and doesn’t include the array of wall-mounted monitors at the front of the control center – the largest of which is a 42’ x 12’ map board.
After considering numerous console options, GSOC ultimately chose Winsted’s Custom Division, for a variety of reasons. One of them was time. The new consoles had to be installed in a very short amount of time and needed to be completed prior to the upgrade of GSOC’s energy control system. Including design time, manufacturing and installation, Winsted was able to meet the strict deadline.
Another reason was location. Winsted’s Custom Division, is a mere 25 minutes away from GSOC, which made it possible for Snyder to go there and see the consoles throughout the manufacturing process. “We like dealing with local vendors, so the fact that Winstead was close made it ideal,” said Snyder. “But if they could have delivered it from Seattle in the timeframe they did, we still would have chosen Winsted.”
Snyder and his team looked at finished products Winsted had built in their own showroom as well as other control centers and liked the clean lines of the consoles. They were complementary with what GSOC had in mind for the modernization of their control centers. “We were trying to get away from old-style, cabinet-like consoles,” said Snyder. “Our previous consoles were made with CRT insets with glass fronts and they couldn’t hold the new flat panel monitors, so they had to go.”
According to Snyder, the new consoles were developed after significant work by Winsted’s design team and the architect for the project. They looked at the control center floor plan, how the existing consoles were laid out and how they could fit everything in and still meet ergonomic and ADA requirements. Because the consoles had to fit in an existing space, Winsted’s ability to do custom Corian work for the work surfaces was something that intrigued Snyder.
Perhaps more important, in terms of ergonomics and functionality, Winsted’s unique Adapt-A-Track monitor mounting system was a significant feature that put them on GSOC’s short list. The post mounting system uses an integrated horizontal aluminum track with easy horizontal adjustment, allowing greater versatility of monitor sizes.
Adapt-A-Track is mounted in a recess behind the console work surface, making it possible to mount the first monitor on the post significantly lower than other consoles. This improves sightlines to monitors mounted to the workstation, reducing eyestrain and neck fatigue, and makes it possible for operators to look over their own workstation to view the monitor wall and map board. “We had to have a way of getting the initial row of monitors low enough so that our operators could look over them and see the big map board,” said Snyder. “Winsted is the only console provider we saw that had that capability.”
With the help of Winsted’s Custom Division, GSOC now has two completely upgraded, ergonomically designed and showpiece-worthy control centers. There are five new workstations in the generation control center. In the transmission control center, there are two engineering consoles and four operating consoles – three of which were designed to be redundant and manned by two operators in the event of severe weather or other emergencies.
“Are we happy with the Winsted consoles? Yes,” said Snyder. “So much so that in the building of our new training center we installed Winsted consoles there, also.”
“Are we happy with the Winsted consoles? Yes — so much so that in the building of our new training center we installed Winsted consoles there, also.”